Top Ways to Improve Safety At Your Workplace in 2024
Workplace safety is a legal matter and the backbone of a thriving organization. According to a National Safety Council press release, employers spent up to $167 billion on workplace injuries alone in 2022. This figure doesn’t even include the millions of days of productivity lost due to these injured employees.
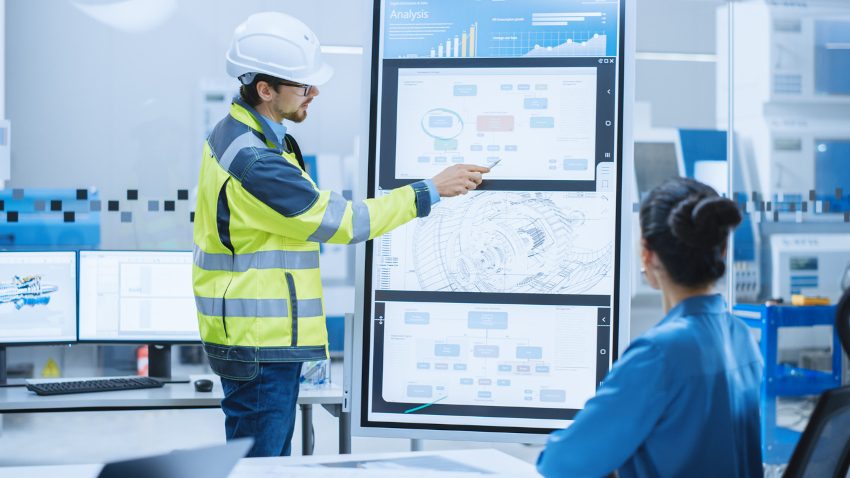
Therefore, when a worker develops an injury or loses their life on the job, it extends beyond monetary considerations. It affects the morale, productivity, and overall well-being of the workforce.
But imagine an environment where every employee feels safe, valued, and heard. An environment where you are healthier and can focus on your work without worry. All these start with developing a safety culture within you through a regular safety training program. Here are other ways in which you can ensure safety at the workplace.
Assess Current Safety Procedures
Did you know that there was a 5% increase in preventable work deaths in 2022? In addition to this, there were also 791 homicides and suicides in the same year. This is according to an overview conducted by Injury Facts in 2022.
While managing a workplace, one of the most critical questions you must address is, “Are the tried-and-true safety practices still effective in the changing workplace?” Or is there a better way of safeguarding employees from accidents and injuries? Preventable deaths would be significantly reduced, and the employees’ safety would improve.
But the main question is: How do you assess current safety procedures, and what are the key areas to focus on to ensure their effectiveness?
These are the areas of safety analysis that you can look at first.
- Risk Assessment: The first step in assessing your safety procedures is reviewing your system’s pressure points. Identify the possible lapses most likely to result in workplace accidents that must be addressed immediately.
- Emergency Response System: Do an in-depth check on the installed emergency response system within your company or job site. Conduct regular checks on how your existing systems will respond to an emergency.
- Equipment Inspection: Regular equipment inspection is also crucial for assessing your safety. This will not only improve your safety but also enhance your general productivity.
Remember always to assess your current safety procedures to ensure the effectiveness of your response to injury and a safe workplace.
Identify Safety Gaps
Ensuring safety at all times in the organization comes with many challenges. However, with a precise safety gap analysis, you can maintain constant safety at your workplace.
Therefore, if you are unsure why your incident figures, compliance, and work safety audit aren’t what they should be, then it is time to conduct a safety gap analysis. The steps to a safety gap analysis are as follows.
- Assess and analyze your future state. Once you have achieved all your safety goals, describe the appearance of your workplace.
- Assess your current situation. After you have outlined your goals, identify the gaps between you and your desired future.
- Identify how you will bridge the gaps. Brainstorm all the possible strategies that you will use to bridge the gap.
You can use the above procedure to solve the current workplace safety issues around you. These issues may involve workplace stress, distractions, ergonomic concerns, falls and tripping hazards, noise-induced issues, and illness transmission. Just follow the procedure to ensure your maximum safety at the workplace.
Develop a Safety Improvement Plan
Improvement of your workplace safety needs a planned, disciplined, and managed approach. With a well-articulated plan, you can establish incremental improvement milestones with a targeted safety improvement goal. It fosters employee communication by providing a common direction and commitment to achieving safety goals. Also, a good safety plan is a mechanism to enhance employee involvement in safety planning and activities.
While developing a safety plan, remember that your main goal is strengthening safety practices and increasing knowledge and awareness. The following steps are crucial to a safety improvement plan.
- Recognize Opportunities for Improvement
Start by considering your current status of safety practices and performance. With the listed areas for possible improvement, identify the high-level goals for safety improvement.
You should consider setting safety goals to achieve within your assessment cycle. These goals should be clearly defined and continuously improved, and injury rates shouldn’t be overemphasized.
- Identify and Prioritize
Place your goals in order of importance and the possibility of achieving them. While doing this, don’t overwhelm the plan with too many actions that will not be achievable, given your current resource capacity. Also, the goals should be made clear and assigned to individuals with the capacity, competencies, and resources to ensure their effectiveness.
- Organize a Plan for Action
The next step is to formulate your goals into organized plans with clear assignments, a timeline for achievement, and a financial budget and resources. Also, include your monitoring action and approach to reviewing progress.
- Communicate the Safety Improvement Plan
With a clear plan and goals, engage your employees and inform them of your expectations, commitment, and effort to improve workplace safety.
Implement Safety Training Programs
An interesting lag exists in organizations’ operational capacity regarding training and implementing programs. Actually, according to a study, 74% of organizations have safety programs, but only 59% have reported effectiveness in their implementation. Most organizations are willing to ensure workplace safety, but only some implement the programs.
These safety programs are essential in ensuring higher efficiency and accident prevention, but they also provide higher employee satisfaction and a better company reputation. Safety training can come in different ways, including induction training, refresher training, and toolbox talks.
The different types of employee safety education can be short and informal, like toolbox talks, or formal, like induction and refresher training.
While designing these programs for your employees, you can refer to the national Environmental, Health, and safety training standards to ensure you deliver the training, evaluate its outcomes, and document its compliance.
Utilize Safety Equipment and Technology
Using technology and safety equipment allows your employees to become more aware of their workplace surroundings and the dangers they may encounter. Technology also offers high-speed communication that improves workplace safety.

One of the best technologies you can use is digital signage. Solutions provided by this technology can help inform and educate your employees by sending information to your displays remotely. This can range from announcements for upcoming trainings, important safety reminders, or even automated emergency alerts.
Regularly Review and Update Procedures
Remember that safety programs keep changing, and to ensure their effectiveness, safety manuals must be regularly updated to reflect changing workplace hazards and processes. To update and revise your manual, familiarize yourself with the safety manuals, review them at least annually, and ensure that all employees know their contents.
Analyze the maintenance of safety procedures and see if they align with your organization’s current and future problems. If not, review and update the safety procedure to ensure that it aligns with your organization’s future goals.
Improve Your Staff Productivity Today
Conducting a risk assessment, formulating a safety management plan, and drafting an effective program can increase productivity and efficiency and improve workplace safety. Ensure that your goals are clear and that you have an effective implementation program.